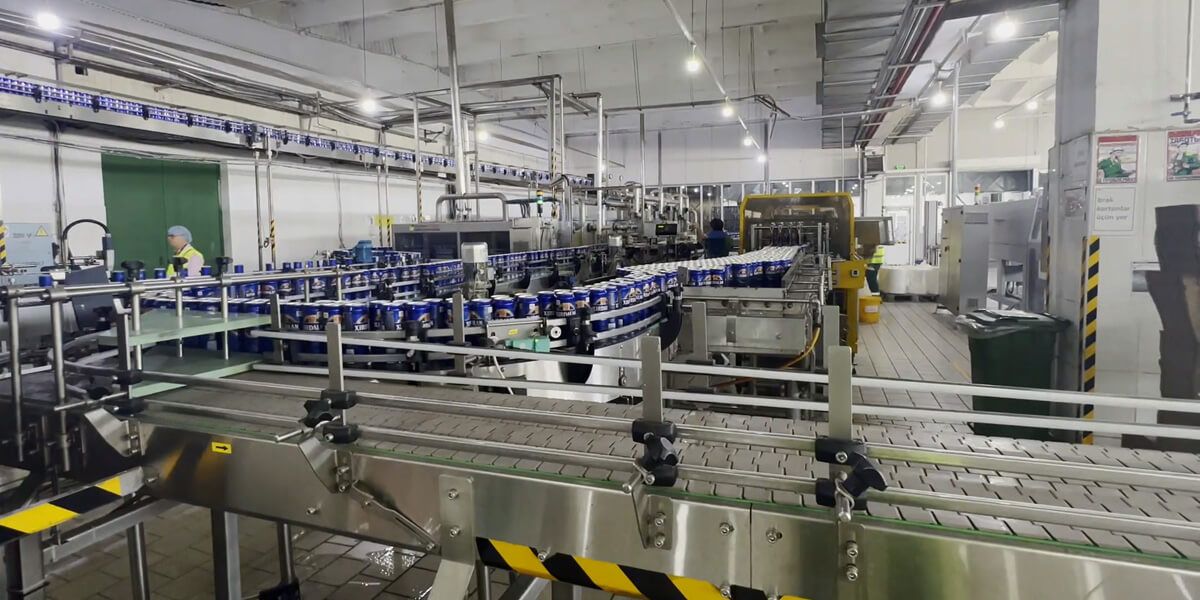
«We were able to purchase two inkjet printers from Arcon, as part of a larger packaging equipment purchase. With an Arcon service contract, we are guaranteed to have an expert, someone who knows what he’s doing and can get the job done right. This means I don’t have to pull one of my staff away from a more important project to fix a coding issue, which is a huge benefit. And the impromptu training helps to increase our institutional knowledge of the equipment, so that we can become more self-sufficient in the future.»
Vugar Akhmedov
Operations Director, Carlsberg Brewery
The Client
Carlsberg Azerbaijan in Baku was founded in 2000. Since then, it has grown into a regional craft brewery, employing over 200 people. It currently brews over 20 beers for distribution, along with a variety of small-batch beers that are shipped throughout the North Caucasus region and beyond.
The Need
As Carlsberg Brewery grew, reliable labelling and coding equipment became necessary to apply date codes to glass bottles, cartons, and five litre containers.
For Carlsberg, flexibility was critical as the company needed to add printers to three different packaging lines: one upstream to code directly onto glass bottles; another to code the outside of cartons before they entered the palletizer; and the final one to code the company’s five-litre line as the containers moved to the filler.
Optimizing the performance of each piece of coding equipment was also crucial. The equipment represented a significant investment in the company’s resources and was expected to be well-maintained and function properly.
The Solution
To address its needs, Carlsberg Brewery acquired labeling and coding equipment from Arcon and actively sought service agreements with Arcon, which is the largest field service organization in the industry in Azerbaijan. Arcon could spend more time on-site, providing preventative maintenance, additional training, and, most importantly, when service is required, Arcon can respond much faster than the competition, helping Carlsberg save on downtime costs.
As part of the service package, Arcon helped Carlsberg seamlessly integrate the inkjet printers into their production line and resolve adaptation issues. The printers produce crisp, high-contrast codes and are ideal for printing on both paper labels applied to bottles and directly onto Carlsberg Brewery’s steel keg canisters. Carlsberg soon realized they needed to expand their coding protocol to print more information on a broader range of materials.
CARLSBERG Leverages the Proactive Service Capabilities of ARCON
Since downtime is costly in the bottling industry, especially when high-speed lines need to run continuously, one of Carlsberg’s first actions after purchasing the printers was to contact Arcon for a service contract. Each Arcon Care Package includes on-site service, preventative visits, additional operator training, and priority services.
By acquiring Arcon service contracts for the three new printers, Carlsberg was able to once again draw on Arcon’s expertise to quickly install the equipment on its production lines and customize the coding parameters for the different applications.
Arcon offers consultative support when the company hires new operators, installs a new production line, receives new coding requirements from its customers, or needs new product coding.
Arcon Care Packages—designed for both new and existing Arcon equipment—help companies stay ahead of maintenance needs with proactive service options. Whether the goal is to minimize downtime or maximize productivity, Arcon offers comprehensive, fixed-cost service and repair solutions.
Arcon’s services include:
- On-site support provided by two certified field service engineers
- Quarterly preventative maintenance visits
- 360° printer health checks for maximum productivity
- Assistance to improve print quality and resolve coding issues
- Year-round priority service to quickly address unexpected needs
- Additional training available for new hires, new applications, and new installations
- 24/7/365 telephone technical support with access to Arcon experts when needed
- Parts management to virtually eliminate parts procurement and inventory management
Arcon's Service Care Package™ provides peace of mind with preventative maintenance, quarterly checks, and service calls.
Carlsberg has chosen the Service Care package from Arcon to ensure their equipment is in optimal condition and to entrust printer maintenance to Arcon's experienced service team.
The Benefits
Over the years, Carlsberg has benefited from various offerings under the Service Care package, including unlimited service visits and 24/7 technical support by phone. The company also benefits from Arcon’s Preventive Maintenance offer, which provides Carlsberg with 360-degree printer health checks to keep equipment in top condition and maximize productivity and output. If a service visit is required, Arcon has a team of two service engineers in the Carlsberg brewery region.
Now, after many years of successful production with well-maintained Arcon equipment, Carlsberg continues to add equipment from Arcon and enjoys all the benefits that the service packages provide.
If you are interested in a similar solution, please fill out the contact form below or email us at
Food / Beverages
Industrial Code Printers, Serialization & Aggregation, Labellers, Continuous Inkjet Printers